لوله های قطورفولادی چیست و چه مصرفی در خطوط انتقال آب ،نفت و گاز دارد؟
بهمن محسن زادگان دارای مدرک کارشناسی مهندسی مکانیک با گرایش طراحی ماشین ( سال ۱۳۵۵ ) از دانشگاه علم و صنعت ایران و کارشناسی ارشد طراحی ماشین با گرایش طراحی ماشین ابزار از دانشگاه امیرکبیر ( سال ۱۳۶۴)است. وی از سال ۱۳۵۳ با صنایع مختلف مانند کاشی و سرامیک ، قالب سازی و ماشین سازی همکاری داشته و پس از پایان دوره خدمت سربازی ، از خرداد ماه ۱۳۵۸ تا تیرماه ۱۳۶۲ در مناطق محروم بلوچستان با سازمان ها و ارگان های منطقه همکاری داشته و همزمان با دفتر طراحی شرکت ماشین سازی اراک، دوره کارشناسی ارشد را نیز طی کرده است.
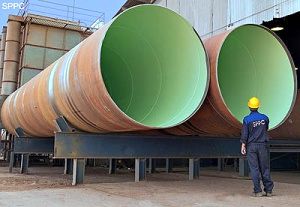
بهمن محسن زادگان دارای مدرک کارشناسی مهندسی مکانیک با گرایش طراحی ماشین ( سال 1355 ) از دانشگاه علم و صنعت ایران و کارشناسی ارشد طراحی ماشین با گرایش طراحی ماشین ابزار از دانشگاه امیرکبیر ( سال 1364)است. وی از سال 1353 با صنایع مختلف مانند کاشی و سرامیک ، قالب سازی و ماشین سازی همکاری داشته و پس از پایان دوره خدمت سربازی ، از خرداد ماه 1358 تا تیرماه 1362 در مناطق محروم بلوچستان با سازمان ها و ارگان های منطقه همکاری داشته و همزمان با دفتر طراحی شرکت ماشین سازی اراک، دوره کارشناسی ارشد را نیز طی کرده است. او همچنین از تیر ماه 1364 در شرکت پروفیل نیمه سبک که به گروه صنعتی سدید تغییر نام داد مشغول بکار شده و در سمت ها و قسمت های مختلفی مانند سر پرست دفتر طراحی ، رییس کارگاه ساخت ، مدیر پروژه ساخت تجهیزات کارخانه فولاد مبارکه و مدیر شیفت کارخانه ماشین سازی مشغول به کار بوده است. محسن زادگان در سال 1369 با توجه به تصمیم مدیریت شرکت مبنی بر خرید و نصب خط تولید لوله های قطور باروش اسپیرال از شرکت HOESH آلمان، به عنوان مدیر فنی پروژه منصوب شد و تا سال 1371 در این زمینه انجام وظیفه کرد. او در سال 1372 به سمت مدیر فنی
شرکت جدید التاسیس لوله و پروفیل سدید منصوب شد که بعدها به شرکت لوله و تجهیزات سدید تغییر نام داد. وی تا سال 1386 در شرکت مذکور در سمت هایی همچون مدیر فنی ، مدیر مهندسی ، مشاور فنی و مهندسی مدیر عامل ، مدیر کارخانه بندر عباس ، مدیر مهندسی فروش و ... مشغول به فعالیت بوده است . همچنین در این مدت در زمینه شناخت استانداردهای حاکم بر لوله های نفت ،گاز ،پتروشیمی و آب در ایران و جهان و محاسبات خطوط لوله و تدوین و بازنگری استانداردهای ملی نیزهمکاری داشته و از آن زمان تاکنون با گروه صنعتی سدید و شرکتهای تابعه همکاری دارد. لوله های قطور، لوله های غیر قطور لوله های قطور معمولا به لوله هایی با قطر خارجی بزرگتر از 20 اینچ ( 500 میلیمتر ) گفته می شود که دارای مصارف و پروژه های زیر بنایی ،خاص و اغلب استراتژیک اند و مشتری اصلی آنها معمولا دولت، سازمانها و نهادهای وابسته به آن هستند.اغلب قریب به اتفاق این لوله ها از ورق و باروش جوشکاری ساخته می شوند، در حالی که لوله های غیر قطور تقریبا در بیشترموارد مصرف دارند و مشتری آن تمامی اقشار جامعه اند. روش های ساخت وتولید لوله، مصارف و کاربرد روش های ساخت وتولید لوله به دو دسته تقسیم
می شود: A) لوله های بدون درز این نوع لوله ها که از قطر خارجی کوچک و دقت بالا، کیفیت خوب و کارایی مناسب و ایمن برخوردار هستند و از نظر جنس شامل لوله های فولادی متداول، لوله آلیاژ، لوله استنلس استیل و... بوده و در صنایع آب ،نفت، گاز، پتروشیمی ،جداره چاه های نفت ،صنایع خودرو سازی، هوا فضا و ... مصرف می گردند ، اساساً به روش های زیر تولید می شوند: 1- تولید لوله از بیلت - در این حالت شمش مبنای تولید لوله پس از گرم شدن تادرجه حرارت تعریف شده، در قالب مربوطه قرار گرفته و یک سنبه از مرکز آن شلیک میگردد تا لوله مورد نظر حاصل شود. پس از تولید، این نوع لوله ها در کوره های مخصوص، تحت عملیات حرارتی و تنش گیری قرار میگیرند. 2- تولید لوله به صورت ریختهگری گریز از مرکز: در این روش ذوب،لوله در مجموعه گریز از مرکز ریخته شده و پس از شکل گیری، از قالب مربوطه تخلیه می گردد. B) لوله های درز دار این نوع لوله ها که از اقطار کوچک تا بزرگ تولید می گردند برای موارد مختلف مانند • خطوط انتقال آب ، نفت ، گاز و پتروشیمی • پایه اسکله و پل • ستون ساختمان ، نرده و مبل • کشتی سازی ، معدن و تونل مصرف شده و با استفاده از ورق و فرم دهی و
جوشکاری تولید میشوند. این لوله ها بر اساس نوع جوشکاری به دو دسته، با استفاده از فلز پر کننده و بدون استفاده از فلز پرکننده تقسیم میگردند. مصطلحترین و پرمصرفترین روش جوش با استفاده از فلز پرکننده، جوش زیر پودری (S.A.W) و پر مصرفترین روش جوش بدون فلز پرکننده جوش مقاومت الکتریکی (E.R.W) است. این لولهها بر اساس فرآیند شکل دهی به روش های زیر تقسیم می شوند: 1- روش فرم دهی در استندهای غلطکی سرد در این روش، کلاف (Coil) پس از باز شدن از استندهای متعدد گذشته و درهر مرحله درصدی از فرم نهایی را میگیرد. پس از مرحله فرم نهایی، لوله به روش جوش مقاومتی ، جوشکاری شده و لوله نهایی حاصل میگردد. در این روش لوله از قطرهای بسیار کوچک مثلاً 5/0 اینچ تا حداکثر 24 اینچ تولید میگردد.. 2- روش فرم دهی سه غلطکی در این روش از ورق به صورت صفحهای (Sheet) استفاده شده و در دستگاه نورد سه غلطکی،آنرا به صورت لوله در آورده و درز جوش به صورت (Tack weld) و به طور پیوسته و باروش GMAW جوش داده میشود که این جوش پاس ریشه را تشکیل میدهد. در مراحل بعدی، درز جوش از داخل و خارج به وسیله دستگاه های جوش زیر پودری (S.A.W) پرشده و سپس با
استفاده از مجموعه (expander) شکل و قطر لوله کامل میگردد. 3- روش فرم دهی U&O در این روش نیز از ورق به صورت صفحهای (Sheet) استفاده شده و ابتدا ورق در پرس U به صورت U درآمده و سپس در پرس O به صورت لوله در میآید. سایر مراحل شامل Tack weld و جوشکاری از داخل و خارج و expander مشابه روش سه غلطکی است. 4- روش فرم دهی JCO در این روش نیز از ورق به صورت صفحهای (Sheet) استفاده شده و ورق در پرس فرم دهی به صورت مرحله به مرحله، شکل دهی شده و تبدیل به لوله میشود. سایر مراحل شاملTack weld و جوشکاری از داخل و خارج و expander مشابه روش سه غلطکی است. - در روش های 1و2و3و4، ورق با عرض تعریف شده وارد سیستم فرم دهی میگردد که عرض مذکور بر اساس قطر لوله تعیین می شود. - در سه روش 2و3و4، ورق با طول معمولاً 12 متری تامین میگردد. 5- روش فرم دهی اسپیرال تولید لوله به روش اسپیرال یکی دیگر از روش های استاندارد تولید لوله در جهان است . در این روش، ورق با گذشتن از یک سری غلتک ها با درزی حلزونی ( اسپیرال ) به شکل لوله در خواهد آمد . برخلاف لولۀ درز مستقیم که قطر لوله بستگی به پهنای ورق دارد، در این روش قطر لوله با تغییر زاویۀ تغذیۀ
اولیۀ ورق تغییر خواهد نمود . با تغییر زاویۀ تغذیه، لوله با قطرهای مختلف تولید می شود، در حالی که در روش درز مستقیم باید کل قالب های خط تولید تعویض شوند . از این رو در روش اسپیرال، لوله با قطرهای مختلف را می توان با هزینۀ کمتری نسبت به درز مستقیم تولید کرد .لوله های اسپیرال به دو روش یک مرحله ای ودو مرحله ای تولید می شوند. - لولۀ اسپیرال یک مرحله ای این روش یکی از متداول ترین روش های تولید لوله در جهان و شکل اولیۀ تولید لولۀ اسپیرال است . مراحل تولید در این روش عبارتند از:آماده سازی ورق، شکل دهی ورق و جوشکاری زیرپودری داخل و خارج. در مرحلۀ آماده سازی ورق، سر ورق ها به یکدیگر جوش داده می شوند و لبۀ ورق پخ زده شده و صاف می شود . اگر عملیات شکل دهی را کامل انجام دهند باید لبۀ ورق پیش خم شود تا از ایجاد برآمدگی های غیر قابل پرس جلوگیری شود. برای جوشکاری درز اسپیرال، ابتدا درز داخلی در موقعیت ساعت 6 توسط دستگاه جوش زیرپودری جوش داده خواهد شد . پاس خارجی نیز در موقعیت ساعت 12 جوش داده خواهد شد . تنظیم مشعل جوشکاری به صورت اتوماتیک انجام می گیرد . پس از جوشکاری درز، لوله برش خورده و به مراحل بعدی منتقل خواهد شد
.سرعت تولید در این روش بر اساس سرعت جوشکاری زیرپودری تعیین می شود. سرعت جوشکاری زیرپودری در حدود1 الی 2.5متر بر دقیقه است، گاهی تا 3 متر بر دقیقه هم می رسد. از آنجا که سرعت جوشکاری زیرپودری محدود است، سرعت تولید در این روش کند است. - لولۀ اسپیرال دو مرحله ای تولید لولۀ اسپیرال دو مرحله ای مانند روش یک مرحله ای است، با این تفاوت که در این روش در حین شکل دهی ورق، درز بوسیلۀ GMAW جوشکاری می شود. این جوش پاس ریشه را تشکیل می دهد. در مراحل بعدی، درز از داخل و خارج چند دستگاه جوش زیرپودری پر می شود. این فرایند چهار مرحلۀ اساسی دارد :آماده سازی ورق ، شکل دهی ورق ، جوش با GMAW وجوش زیرپودری داخلی وخارجی. در روش دو مرحله ای علاوه بر راندمان تولید بالا ( به دلیل شکل دهی سریع) ، یک مزیت تکنیکی به لحاظ جدا بودن مرحلۀ شکل دهی و جوش نهایی از یکدیگر وجود دارد. در ایستگاه شکل دهی در حین شکل دهی پای ریشه با روش GMAW جوش داده می شود. سرعت این دستگاه با سیستم گاز محافظ گاز کربنیک در حدود 12 متر بر دقیقه است. این جوش در موقعیت ساعت 6 ایجاد می شود.
ارسال نظر