نگاهی به صنعت CNG
گاز طبیعی فشرده شدهCompressed Natural Gas که به صورت اختصاری CNG خوانده میشود نوعی سوخت فسیلی است که به عنوان جانشینی با آلایندگی کمتر برای سایر سوختهای فسیلی نظیر بنزین و گازوییل در نظر گرفته میشود. CNG با فشردن گاز طبیعی (۷۰ تا ۹۸ درصد متان) بدست میآید و جهت مصرف به عنوان سوخت در مخازن کروی بسیار سخت نگهداری و عرضه میشود.
کروی بودن این مخزنها سبب تقسیم فشار گاز به طور مساوی بین دیوارههای مخزن میشود، که این خود ایمنی بالایی رادر نگهداری حجم بالایی از CNG در مخازن ممکن میکند.
کروی بودن این مخزنها سبب تقسیم فشار گاز به طور مساوی بین دیوارههای مخزن میشود، که این خود ایمنی بالایی رادر نگهداری حجم بالایی از CNG در مخازن ممکن میکند.
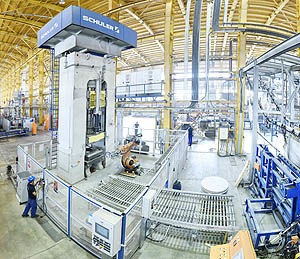
گاز طبیعی فشرده شدهCompressed Natural Gas که به صورت اختصاری CNG خوانده میشود نوعی سوخت فسیلی است که به عنوان جانشینی با آلایندگی کمتر برای سایر سوختهای فسیلی نظیر بنزین و گازوییل در نظر گرفته میشود. CNG با فشردن گاز طبیعی (70 تا 98 درصد متان) بدست میآید و جهت مصرف به عنوان سوخت در مخازن کروی بسیار سخت نگهداری و عرضه میشود.
کروی بودن این مخزنها سبب تقسیم فشار گاز به طور مساوی بین دیوارههای مخزن میشود، که این خود ایمنی بالایی رادر نگهداری حجم بالایی از CNG در مخازن ممکن میکند.افزایش روز افزون وسایل حمل و نقل عمومیو خصوصی، با توجه به نیاز گسترده زندگی شهری به جابجایی سریعتر و افزایش آلودگی زیست محیطی ناشی از سوختهای بنزینی گازوئیلی، برای زندگی شهری به معضلی اساسی بدل شده است. چارهاندیشی برای حل مساله آلودگی محیط طبیعی و شهری، در سراسر دنیا برنامهریزان و دولت مردان را به سوی سرمایهگذاری و استفاده از سوختهای سالم با آلایندگی کمتر هدایت کرد.در ایران نیز با افزایش وسایل حمل و نقل و توسعه صنایع به ویژه بعد از انقلاب و به خصوص در کلان شهرها سطح آلودگی هوا به میزان قابل توجهی افزایش یافته به گونهای که حل مساله آلودگی هوا در دو دهه اخیر از مهمترین مسائل برنامهریزان شهری بوده است.
***
محیط زیست و CNG
همان گونه که گفته شد با وجود این که وسایل نقلیه به عنوان یکی از مهمترین ارکان جامعه صنعتی به شمار میروند، خود سبب ساز جدی ترین معضلات زیست محیطی امروز بشر شدهاند؛ چرا که با تولید دی اکسید کربن، دی اکسید نیتروژن و ذرات آلی غیر قابل تجزیه، تحت اثر اشعه خورشید، گاز ازن ایجاده کرده و به این ترتیب به عمدهترین آلاینده هوا بدل شدهاند.
در فصل تابستان گاز دی اکسید نیتروژن آسمان را قهوه ای رنگ میسازد؛ این وضعیتی است که بسیاری از شهرها با آن مواجه هستند. ذرات ریزحاصل از سوخت موتورهای بنزینی آلودگی و پدیده وارونگی هوا در روزهای زمستانی را به بار میآورند. آلودگی هوای ناشی از سوخت باعث تحریک مجاری تنفسی و تشدید آسم میشود و هر چه میزان ازت موجود دراکسیژن تنفسی بیشتر باشد، تعداد بیشتری از افراد مبتلا به آسم میشوند. تنگی نفس، حملات قلبی و آلرژیهای مختلف تنفسی شایعترین مراجعات پزشکی در روزهای تشدید آلودگی به شمار میروند.
اعلام خطر سازمان محیط زیست، وزارت بهداشت و ارگانهای مرتبط نسبت به چنین وضعیتی نقش اساسی در هدایت مسوولین به استفاده ازسوختهای سالم داشته است.از پاک ترین سوختهای سالم با توجه به اعلام سازمان جهانی بهداشت سلامت، سوخت CNG است .در چنین شرایطی سهامداران شرکت آسیاناما ANCC، تصمیم گرفتند که به وظیفه انسانی خود در قبال جامعه عمل نموده و با سرمایهگذاری در صنعت CNG گامیمهم در زمینه جایگزینی سوخت پاک برداشته و با تمام توان فنی و مدیریتی خود،یکی از بزرگترین کارخانههای تولید مخازن را در منطقه ایجاد نمایند. به امید آنکه در کنار سایر راهکارها از جمله استفاده از وسایل نقلیه عمومی، معاینه فنی وسایل نقلیه، گسترش فضای سبز و اصلاح فرهنگ مصرف، «دوگانه سوز نمودن خودروها» تاثیر به سزایی در برقراری آسمان آبی و هوای پاک بر بلندای ایران عزیز اسلامیداشته باشد.
امروزه استفاده از این نوع سوخت در وسایل نقلیه عمومیدر حال گسترش است. با توجه به مزایای اقتصادی و دیگر مزایای بر شمرده برای گاز طبیعی، انجمن انرژی جهان نیز از سال 1995 در توکیو گازطبیعی را رسماً به عنوان سوخت جایگزین سوختهای حمل و نقل اعلام نمود.
CNG در ایران
شروع استفاده از سوخت گاز طبیعی فشرده در ایران به سال ۱۳۵۶باز میگردد.در آن سال ۱۰۰۰ دستگاه تاکسی پیکان در شهر شیراز به این نوع سوخت مجهز شده و دو جایگاه سوختگیری نیز ساخته شد. یک سال بعد در شهر مشهد ۶۰۰ دستگاه تاکسی به این نوع سیستم سوخت مجهز شده و یک جایگاه سوختگیری نیز افتتاح گردید.
پس از پیروزی انقلاب در سال ۱۳۷۰ شرکت واحد موتور وابسته به شرکت اتوبوسرانی تهران تعدادی از اتوبوسهای خود را به این نوع سوخت مجهز کرد و سپس در سال ۱۳۷۸ همزمان با تغییر الگوی سوخت کشور توسط دولت در جهت استفاده از گاز طبیعی فشرده به عنوان مناسبترین سوخت جایگزین بنزین، استفاده از این سوخت مورد توجه قرار گرفت. با تاسیس سازمان بهینه سازی مصرف سوخت کشور در سال ۱۳۷۹ در مجموعه وزارت نفت، مطالعات مقدماتی طرح گازسوز نمودن خودروها در این سازمان انجام و به منظور دستیابی به کاهش مصرف بنزین و کاهش آلایندههای هوا، طرح مزبور با انعقاد قراردادهایی با خودروسازان و بخش خصوصی برای تولید و تبدیل خودروهای گازسوز از یک طرف و هم چنین ایجاد زیرساختهای لازم و احداث جایگاههای CNG از طرف دیگر، وارد مرحله اجرایی گردید.
شرکت آسیاناما و تولید مخازن CNG
گروه کارخانجات آسیاناما (سهامیعام) در سال ۱۳۸۵ در قالب شرکت آسیا ناما با بررسی نیاز بازار داخلی و جهانی و تحقیقات گسترده علمیو صنعتی، با توجه به آلودگی هوای کشور، کمبود سوخت خودرو و برنامه مدون دوگانه سوز نمودن، بر آن شد تا در چارچوب طرح توسعه خود اقدام به تولید مخازن گاز طبیعی فشرده نماید. شرکت آسیاناما با همکاری و سرمایهگذاری گروه سرمایهگذاری امید، عمده ترین سهامدار شرکت آسیاناما تحت نظارت و هدایت بانک سپه جمهوری اسلامی و تشکیل تیم تحقیقاتی و با بهرهگیری از مهندسان و مشاوران برتر داخلی و خارجی و بازار سنجی در ایران و کشورهای همسایه، مصمم به راهاندازی و نصب تجهیزات مربوط به تولید مخزن به روش تولید از ورق و لوله بر اساس استانداردهای ایزو ۱۱۴۳۹ ECE-R-۱۱۰ و ISIRI۷۵۹۸ گردید و تولید سالانه ۳۰۰هزار مخزن گاز طبیعی فشرده CNG با دو دیدگاه انسانی و اقتصادی برای استفاده در خودروهای سواری، وانت، مینی بوس و اتوبوس را در دستور کار قرار داد.
پس از تصویب سازمان بهینهسازی سوخت و وزارت نفت جهت جایگزینی سوخت CNG به جای بنزین در ناوگان حمل و نقل کشوری به منظور کاهش آلودگی، کاهش واردات بنزین و از طرفی کاهش خروج ارز و استفاده از منابع داخلی، شرکت آسیا ناما وابسته به بانک سپه بر آن شد تا با طراحی پروژه برای خودکفایی با تولید ۳۰۰ هزار مخزن در سال، کارخانه ساخت مخازن CNG را در کشور احداث نماید و پیرو آن پروژه آسیاناما در سال ۸۶ با ۸۰۰ هزار میلیون ریال اعتبار ریالی و ۴۰ میلیون دلار اعتبار ارزی در زمینی به مساحت ۳.۷ هکتار و زیربنای ۳ هکتار سوله فلزی آغاز گردید. سرانجام شرکت در سال ۹۱ با سرمایه ۴.۵۰۰هزار میلیون ریال راهاندازی گردید.
شرکت فابر ایتالیا با ظرفیت تولید ۱.۷۰۰.۰۰۰ مخزن در سال، شرکت مت برزیل با ۱۴۰۰۰۰۰ مخزن و شرکت ENK با۱۲۰۰۰۰۰ مخزن در سال در چند نمایندگی تولیدی خود در سرتاسر دنیا و با سه روش متداول تولید مخزن جزو بزرگترین و معروفترین برندهای تولید مخزن در دنیا میباشند.
شرکت آسیاناما نیز با ظرفیت 300000 مخزن در سال و با قابلیت تولید از ورق، بزرگترین تولید کننده مخزن CNG در خاورمیانه است که این تعداد مخزن را بطور متمرکز در یک واحد و از یک روش تولید مینماید. افزون بر این شرکت توانایی تولید 200000 مخزن در سال به روش تولید مخزن از لوله را نیز دارا میباشد.
شناسایی شرکتهای معتبر سازنده دستگاههای تولید و استفاده از تکنولوژی روز دنیا از اولویتهای فنی شرکت بوده است.از همینرو خرید و استفاده از دستگاههای پرس پیشرفته (از شرکت شولر آلمان) با ظرفیتهای 1900 تن ،1200 تن و 800 تن، هم چنین استفاده از دستگاه SPINNING و پیشرفته ترین دستگاه اسپین ENK روتراشی و کف تراشی و رزوهزنی RASOMA متعلق به برندهای مطرح جهان کیفیت تولید مخازن را در آسیاناما به شکل قابل توجهی افزایش داده است.
مزایای CNG
CNG یا همان گاز طبیعی فشرده (Compressed Natural Gas) سوختی است که عمدتا به عنوان جایگزینی برای بنزین، گازوئیل و گاز مایع به کار میرود ودر مقایسه آلودگی کمتری ایجاد میکندو با توجه به سبک تر بودن آن نسبت به هوا و سرعت پراکنده شدن آن ایمنی بیشتری در هنگام نشت دارد. CNG در خودروهای بنزینسوز ،که موتور آنها برای استفاده از CNG اصلاح شده و خودروهایی که با موتور اختصاصا CNG سوز ساخته شدهاند، استفاده میشود. در سال ۲۰۱۳ بیش از ۱۸ میلیون خودرو سیانجی فعال بودهاند. ایران بزرگترین ناوگان خودروهای CNG سوز را با ۳.۵ میلیون در اختیار داشتهاست. پاکستان و آرژانتین با بیش از دو میلیون و برزیل، چین و هند با بیش از یک و نیم میلیون خودروی CNG سوز در رتبههای بعد قرار دارند.
در مجموع عمدهترین مزایایی که کارشناسان سوخت برای CNG بر میشمرند به قرار زیر است:
*برخلاف بنزین و گازوئیل خطر شکلگیری رسوب، انفجار یا جرقه رفع شده است.
*کاهش میزان خسارات ناشی از تبخیر سوخت در سیستم سوخت CNG تایید شده است.
*باعث افزایش طول عمر روغن خودرو است.
* CNG توسط سایر عوامل آلوده نمیشود، در نتیجه میل لنگ روغن آلوده نشده و طول عمر آن افزایش مییابد.
* CNG سریع و بهآسانی با هوا ترکیب میشود چرا که سوخت گازی است.
*CNG کمترین میزان گازهای خطرناک نظیر دی اکسید کربن، هیدروکربن UHC و مونوکسید کربن CO CO2را هنگام سوختن ایجاد میکند.حال آنکه موتورهای بنزینی میزان 22000 گرم CO2 در هر 100 کیلومتر ایجاد مینماید که میزان آن در CNG تنها 275/ 16 گرم است.
* CO۲آزاد شده از نفت ۴۰درصد بیشتر از CO۲ آزاد شده CNG است. مهمتر آنکه، طی این پروسه نفت ۶/ ۱ برابر بیشتر نیاز به انرژی دارد. به دلیل کاهش میزان مونوکسید کربن و اکسید نیتروس، استفادهCNG خدمت بزرگی برای حفظ فضای سبز در زمین است. به هر جهت آلوده کنندگی بنزین در مقایسه با CNG بسیار بیشتر است.
*عدد اکتان بالا (۱۳۰) با افزایش راندمان ۱۵ درصدی در بهرهوری از سوخت. چگالی انرژی سیانجی ۴۲ درصد گاز طبیعی مایعشده و ۲۵ درصد گازوئیل است و در نتیجه در حجم مساوی یکچهارم گازوئیل انرژی تولید میکند.
انواع مخازن CNG
گاز طبیعی که به عنوان سوخت در خودروها مورد استفاده قرار میگیرد با توجه به دانسیته انرژی کم آن نیاز به فشردهسازی تا ۲۰۰ برابر سطح فشار معمول خود دارد تا امکان سوخت رسانی به خودرو برای مسافتهای طولانیتر را داشته باشد. با وجود چنین فشار بالایی در سیستم سوخت رسانی CNG مخازن فلزی یا کامپوزیت که برای این فشار عملیاتی طراحی شدهاند الزامات ایمنی بالایی را ایجاب میکند. مخازن تولید شده با چنین امکانی در جهان اصولا به چهار دسته تقسیم میشوند:
- نوع اول تمام فلزی
- نوع دوم با آستر فلزی و ۴۵درصد کامپوزیت
- نوع سوم با آستر فلزی و 80درصد کامپوزیت
- نوع چهارم صد درصد کامپوزیت
انواع روشهای تولید مخزن
همان گونه که در زیر خواهد آمد تولید مخازن نوع اول به سه روش انجام می گیرد. شرکت آسیا ناما قادر به تولید مخازن به دوشیوه از سه شیوه ممکن است که به اختصار روش تولید هر کدام از شیوهها اشاره خواهد شد.
روش اول:
1- استفاده از شمش(billet)
در این روش تولید مخازن CNG، شمش فولادی از طریق فرایند اکستروژن به صورت کاپ در آمده و سپس سر این کاپها توسط فرایند فرم دهی گرم شکل دهی میگردد.
2- استفاده از لوله (pipe)
در این روش پس از بریدن لوله خام به اندازههای مورد نیاز، انتها و سر لوله توسط فرایند فرمدهی گرم شکلدهی میشود.
3- استفاده از ورق (plate)
در این روش تولید مخازن CNG ابتدا یک ورق گرد به اندازه مورد نیاز بریده شده و سپس توسط پرسهایی در چندین مرحله مورد کشش عمیق (کشش سرد) قرار میگیرد و کاپ تولید میگردد. سپس توسط فرایند فرمدهی گرم سر این کاپها بسته میشود.
مزیت تولید مخزن از ورق
استفاده از ورق برای تولید مخازن بدون درز CNG با روش فوق مزایایی را در بر دارد که در این قسمت به آنها اشاره میکنیم.
با توجه به روش تولید و مواد اولیه مورد نیاز، مزایای تولید مخازن با استفاده از ورق عبارتند از:
امکان استفاده از خط تولید با فناوری قابل دسترس جهت تولید بدنه استوانهای شکل:
خط تولید در این روش عموما از پرسهای هیدرولیک و قالبهای کشش تشکیل میشود و در حال حاضر صنایع مختلف فعال در کشور از این تجهیزات استفاده نموده و حتی قابلیت تولید آن را نیز دارند.
امکان تهیه مواد اولیه در داخل کشور: هم اکنون صنایع فولاد سازی انواع ورقهای مختلف را تولید میکنند و امکان تولید ورقهای مورد نیاز در کشور میسر است.
قابلیت انبارش بیشتر مواد اولیه: نظر به این که امکان قرار دادن ورقهای فولادی به صورت بستهای روی یکدیگر بیشتر از سایر مواد اولیه میباشد، در این روش به مساحت انبار کمتری نیاز میباشد.
امکان جابهجایی و حمل و نقل آسان تر مواد اولیه: با توجه به این که امکان جا به جایی و راندمان حمل و نقل ورقهای فولادی بالاتر از لولههای بدون درز میباشد هزینه حمل و نقل خارج از کارخانه کمتر بوده و جابهجایی آنها در داخل کارخانه نیز با سهولت بیشتری انجام خواهد شد.
ارزانتر بودن مواد اولیه: با توجه به این که تولید لولههای فولادی بدون درز مورد استفاده در ساخت مخازن در انحصار چند شرکت معدود خارجی میباشد، امکان تهیه ارزانتر ورقهای فولادی در داخل و یا حتی واردات آنها با بهای کمتر وجود دارد.
امکان دست یابی به دقتهای بالاتر در محصولات: نظر به این که خط تولید در این روش صرفا جهت تولید مخازن CNG طراحی میشود و در مقابل تولید کنندگان لولههای بدون درز محصولات خود را جهت استفادههای عام تولید میکنند، تلرانسهای مد نظر در استانداردهای تولید این مخازن در روش تولید با ورق کاملا قابل رعایت است.
امکان تولید کاپ به عنوان مواد اولیه کارخانجات کشور
با توجه به عدم نیاز به واردات لوله به عنوان مواد اولیه، خودکفایی در زمینه تولید این محصول فراهم میگردد.
سبکتر بودن مخازن تولید شده: در این روش امکان دسترسی به حداقل ضخامت استاندارد جداره مخازن به علت بستهتر بودن تلرانسهای اعمال شده بر پروفیل مخازن بیشتر است. لذا مخازن تولید شده دارای وزن کمتری نسبت به نوع مشابه تولید شده ازلوله میباشند. از آنجا که سبک تر بودن مخازن استفاده شده در خورو دارای مزایا فراوانی است تولید با این روش مناسبتر میباشد. از مزایای سبک تر بودن مخازن میتوان به موارد زیر اشاره نمود:
کاهش مصرف ترمز خودرو
کاهش مصرف سوخت
بهبود سیستم تعلیق خودرو
یکنواختی ضخامت به علت کشش عمیق در تولید مخازن از ورق (در ورق نوسان ضخامت ۰.۲ میلیمتر و در لوله ۰.۶ میلیمتر میباشد).
حداقل استحکام کششی قابل حصول در مخازن تولیدی از ورق: 1000 مگاپاسکال
حداقل استحکام کششی قابل حصول در مخازن تولیدی از لوله: ۹۵۵مگاپاسکال
عدم نشتی از انتهای مخزن را میتوان به عنوان یکی از مهمترین مزیتهای روش تولید از ورق در تولید این نوع مخازن نام برد. به همین خاطر در استاندارد ISO ۱۱۴۳۹ در روش تولیدی از لوله، به دلیل فرم دهی انتهای مخزن، سازنده را ملزم به تستهای غیر مخرب نموده است، ولی در روش تولیدی از ورق به دلیل بالا بودن اطمینان از عدم نشتی و بالا بودن ایمنی نیازی به این تست نمیباشد.استاندارد ISO ۱۱۴۳۹ یک تست پنوماتیکی را برای مخازن تولیدی از لوله به دلیل فرم دهی گرم انتهای مخزن در نظر گرفته است که طبق آن میبایست حد اقل ۲/ ۳ فشار کاری مخزن با هوا تست گردد در صورتی که برای مخازن تولیدی از ورق به این تست نیازی نمیباشد.
مقایسه کیفیت تولید مخازن تولیدی از روش لوله و ورق
اطمینان از ۱۰۰درصد عدم نشتی مخزن از انتها در روش تولید از ورق
انتهای مخازن تولیدی از ورق با کیفیت بالا و بدون نیاز به پروسههای اضافی جهت یکنواخت کردن انتهای مخزن
انتهای مخازن تولیدی از لوله نیاز به پروسههای اضافی جهت یکنواخت کردن انتهای مخزن و زائدههای آن ندارد.
کروی بودن این مخزنها سبب تقسیم فشار گاز به طور مساوی بین دیوارههای مخزن میشود، که این خود ایمنی بالایی رادر نگهداری حجم بالایی از CNG در مخازن ممکن میکند.افزایش روز افزون وسایل حمل و نقل عمومیو خصوصی، با توجه به نیاز گسترده زندگی شهری به جابجایی سریعتر و افزایش آلودگی زیست محیطی ناشی از سوختهای بنزینی گازوئیلی، برای زندگی شهری به معضلی اساسی بدل شده است. چارهاندیشی برای حل مساله آلودگی محیط طبیعی و شهری، در سراسر دنیا برنامهریزان و دولت مردان را به سوی سرمایهگذاری و استفاده از سوختهای سالم با آلایندگی کمتر هدایت کرد.در ایران نیز با افزایش وسایل حمل و نقل و توسعه صنایع به ویژه بعد از انقلاب و به خصوص در کلان شهرها سطح آلودگی هوا به میزان قابل توجهی افزایش یافته به گونهای که حل مساله آلودگی هوا در دو دهه اخیر از مهمترین مسائل برنامهریزان شهری بوده است.
***
محیط زیست و CNG
همان گونه که گفته شد با وجود این که وسایل نقلیه به عنوان یکی از مهمترین ارکان جامعه صنعتی به شمار میروند، خود سبب ساز جدی ترین معضلات زیست محیطی امروز بشر شدهاند؛ چرا که با تولید دی اکسید کربن، دی اکسید نیتروژن و ذرات آلی غیر قابل تجزیه، تحت اثر اشعه خورشید، گاز ازن ایجاده کرده و به این ترتیب به عمدهترین آلاینده هوا بدل شدهاند.
در فصل تابستان گاز دی اکسید نیتروژن آسمان را قهوه ای رنگ میسازد؛ این وضعیتی است که بسیاری از شهرها با آن مواجه هستند. ذرات ریزحاصل از سوخت موتورهای بنزینی آلودگی و پدیده وارونگی هوا در روزهای زمستانی را به بار میآورند. آلودگی هوای ناشی از سوخت باعث تحریک مجاری تنفسی و تشدید آسم میشود و هر چه میزان ازت موجود دراکسیژن تنفسی بیشتر باشد، تعداد بیشتری از افراد مبتلا به آسم میشوند. تنگی نفس، حملات قلبی و آلرژیهای مختلف تنفسی شایعترین مراجعات پزشکی در روزهای تشدید آلودگی به شمار میروند.
اعلام خطر سازمان محیط زیست، وزارت بهداشت و ارگانهای مرتبط نسبت به چنین وضعیتی نقش اساسی در هدایت مسوولین به استفاده ازسوختهای سالم داشته است.از پاک ترین سوختهای سالم با توجه به اعلام سازمان جهانی بهداشت سلامت، سوخت CNG است .در چنین شرایطی سهامداران شرکت آسیاناما ANCC، تصمیم گرفتند که به وظیفه انسانی خود در قبال جامعه عمل نموده و با سرمایهگذاری در صنعت CNG گامیمهم در زمینه جایگزینی سوخت پاک برداشته و با تمام توان فنی و مدیریتی خود،یکی از بزرگترین کارخانههای تولید مخازن را در منطقه ایجاد نمایند. به امید آنکه در کنار سایر راهکارها از جمله استفاده از وسایل نقلیه عمومی، معاینه فنی وسایل نقلیه، گسترش فضای سبز و اصلاح فرهنگ مصرف، «دوگانه سوز نمودن خودروها» تاثیر به سزایی در برقراری آسمان آبی و هوای پاک بر بلندای ایران عزیز اسلامیداشته باشد.
امروزه استفاده از این نوع سوخت در وسایل نقلیه عمومیدر حال گسترش است. با توجه به مزایای اقتصادی و دیگر مزایای بر شمرده برای گاز طبیعی، انجمن انرژی جهان نیز از سال 1995 در توکیو گازطبیعی را رسماً به عنوان سوخت جایگزین سوختهای حمل و نقل اعلام نمود.
CNG در ایران
شروع استفاده از سوخت گاز طبیعی فشرده در ایران به سال ۱۳۵۶باز میگردد.در آن سال ۱۰۰۰ دستگاه تاکسی پیکان در شهر شیراز به این نوع سوخت مجهز شده و دو جایگاه سوختگیری نیز ساخته شد. یک سال بعد در شهر مشهد ۶۰۰ دستگاه تاکسی به این نوع سیستم سوخت مجهز شده و یک جایگاه سوختگیری نیز افتتاح گردید.
پس از پیروزی انقلاب در سال ۱۳۷۰ شرکت واحد موتور وابسته به شرکت اتوبوسرانی تهران تعدادی از اتوبوسهای خود را به این نوع سوخت مجهز کرد و سپس در سال ۱۳۷۸ همزمان با تغییر الگوی سوخت کشور توسط دولت در جهت استفاده از گاز طبیعی فشرده به عنوان مناسبترین سوخت جایگزین بنزین، استفاده از این سوخت مورد توجه قرار گرفت. با تاسیس سازمان بهینه سازی مصرف سوخت کشور در سال ۱۳۷۹ در مجموعه وزارت نفت، مطالعات مقدماتی طرح گازسوز نمودن خودروها در این سازمان انجام و به منظور دستیابی به کاهش مصرف بنزین و کاهش آلایندههای هوا، طرح مزبور با انعقاد قراردادهایی با خودروسازان و بخش خصوصی برای تولید و تبدیل خودروهای گازسوز از یک طرف و هم چنین ایجاد زیرساختهای لازم و احداث جایگاههای CNG از طرف دیگر، وارد مرحله اجرایی گردید.
شرکت آسیاناما و تولید مخازن CNG
گروه کارخانجات آسیاناما (سهامیعام) در سال ۱۳۸۵ در قالب شرکت آسیا ناما با بررسی نیاز بازار داخلی و جهانی و تحقیقات گسترده علمیو صنعتی، با توجه به آلودگی هوای کشور، کمبود سوخت خودرو و برنامه مدون دوگانه سوز نمودن، بر آن شد تا در چارچوب طرح توسعه خود اقدام به تولید مخازن گاز طبیعی فشرده نماید. شرکت آسیاناما با همکاری و سرمایهگذاری گروه سرمایهگذاری امید، عمده ترین سهامدار شرکت آسیاناما تحت نظارت و هدایت بانک سپه جمهوری اسلامی و تشکیل تیم تحقیقاتی و با بهرهگیری از مهندسان و مشاوران برتر داخلی و خارجی و بازار سنجی در ایران و کشورهای همسایه، مصمم به راهاندازی و نصب تجهیزات مربوط به تولید مخزن به روش تولید از ورق و لوله بر اساس استانداردهای ایزو ۱۱۴۳۹ ECE-R-۱۱۰ و ISIRI۷۵۹۸ گردید و تولید سالانه ۳۰۰هزار مخزن گاز طبیعی فشرده CNG با دو دیدگاه انسانی و اقتصادی برای استفاده در خودروهای سواری، وانت، مینی بوس و اتوبوس را در دستور کار قرار داد.
پس از تصویب سازمان بهینهسازی سوخت و وزارت نفت جهت جایگزینی سوخت CNG به جای بنزین در ناوگان حمل و نقل کشوری به منظور کاهش آلودگی، کاهش واردات بنزین و از طرفی کاهش خروج ارز و استفاده از منابع داخلی، شرکت آسیا ناما وابسته به بانک سپه بر آن شد تا با طراحی پروژه برای خودکفایی با تولید ۳۰۰ هزار مخزن در سال، کارخانه ساخت مخازن CNG را در کشور احداث نماید و پیرو آن پروژه آسیاناما در سال ۸۶ با ۸۰۰ هزار میلیون ریال اعتبار ریالی و ۴۰ میلیون دلار اعتبار ارزی در زمینی به مساحت ۳.۷ هکتار و زیربنای ۳ هکتار سوله فلزی آغاز گردید. سرانجام شرکت در سال ۹۱ با سرمایه ۴.۵۰۰هزار میلیون ریال راهاندازی گردید.
شرکت فابر ایتالیا با ظرفیت تولید ۱.۷۰۰.۰۰۰ مخزن در سال، شرکت مت برزیل با ۱۴۰۰۰۰۰ مخزن و شرکت ENK با۱۲۰۰۰۰۰ مخزن در سال در چند نمایندگی تولیدی خود در سرتاسر دنیا و با سه روش متداول تولید مخزن جزو بزرگترین و معروفترین برندهای تولید مخزن در دنیا میباشند.
شرکت آسیاناما نیز با ظرفیت 300000 مخزن در سال و با قابلیت تولید از ورق، بزرگترین تولید کننده مخزن CNG در خاورمیانه است که این تعداد مخزن را بطور متمرکز در یک واحد و از یک روش تولید مینماید. افزون بر این شرکت توانایی تولید 200000 مخزن در سال به روش تولید مخزن از لوله را نیز دارا میباشد.
شناسایی شرکتهای معتبر سازنده دستگاههای تولید و استفاده از تکنولوژی روز دنیا از اولویتهای فنی شرکت بوده است.از همینرو خرید و استفاده از دستگاههای پرس پیشرفته (از شرکت شولر آلمان) با ظرفیتهای 1900 تن ،1200 تن و 800 تن، هم چنین استفاده از دستگاه SPINNING و پیشرفته ترین دستگاه اسپین ENK روتراشی و کف تراشی و رزوهزنی RASOMA متعلق به برندهای مطرح جهان کیفیت تولید مخازن را در آسیاناما به شکل قابل توجهی افزایش داده است.
مزایای CNG
CNG یا همان گاز طبیعی فشرده (Compressed Natural Gas) سوختی است که عمدتا به عنوان جایگزینی برای بنزین، گازوئیل و گاز مایع به کار میرود ودر مقایسه آلودگی کمتری ایجاد میکندو با توجه به سبک تر بودن آن نسبت به هوا و سرعت پراکنده شدن آن ایمنی بیشتری در هنگام نشت دارد. CNG در خودروهای بنزینسوز ،که موتور آنها برای استفاده از CNG اصلاح شده و خودروهایی که با موتور اختصاصا CNG سوز ساخته شدهاند، استفاده میشود. در سال ۲۰۱۳ بیش از ۱۸ میلیون خودرو سیانجی فعال بودهاند. ایران بزرگترین ناوگان خودروهای CNG سوز را با ۳.۵ میلیون در اختیار داشتهاست. پاکستان و آرژانتین با بیش از دو میلیون و برزیل، چین و هند با بیش از یک و نیم میلیون خودروی CNG سوز در رتبههای بعد قرار دارند.
در مجموع عمدهترین مزایایی که کارشناسان سوخت برای CNG بر میشمرند به قرار زیر است:
*برخلاف بنزین و گازوئیل خطر شکلگیری رسوب، انفجار یا جرقه رفع شده است.
*کاهش میزان خسارات ناشی از تبخیر سوخت در سیستم سوخت CNG تایید شده است.
*باعث افزایش طول عمر روغن خودرو است.
* CNG توسط سایر عوامل آلوده نمیشود، در نتیجه میل لنگ روغن آلوده نشده و طول عمر آن افزایش مییابد.
* CNG سریع و بهآسانی با هوا ترکیب میشود چرا که سوخت گازی است.
*CNG کمترین میزان گازهای خطرناک نظیر دی اکسید کربن، هیدروکربن UHC و مونوکسید کربن CO CO2را هنگام سوختن ایجاد میکند.حال آنکه موتورهای بنزینی میزان 22000 گرم CO2 در هر 100 کیلومتر ایجاد مینماید که میزان آن در CNG تنها 275/ 16 گرم است.
* CO۲آزاد شده از نفت ۴۰درصد بیشتر از CO۲ آزاد شده CNG است. مهمتر آنکه، طی این پروسه نفت ۶/ ۱ برابر بیشتر نیاز به انرژی دارد. به دلیل کاهش میزان مونوکسید کربن و اکسید نیتروس، استفادهCNG خدمت بزرگی برای حفظ فضای سبز در زمین است. به هر جهت آلوده کنندگی بنزین در مقایسه با CNG بسیار بیشتر است.
*عدد اکتان بالا (۱۳۰) با افزایش راندمان ۱۵ درصدی در بهرهوری از سوخت. چگالی انرژی سیانجی ۴۲ درصد گاز طبیعی مایعشده و ۲۵ درصد گازوئیل است و در نتیجه در حجم مساوی یکچهارم گازوئیل انرژی تولید میکند.
انواع مخازن CNG
گاز طبیعی که به عنوان سوخت در خودروها مورد استفاده قرار میگیرد با توجه به دانسیته انرژی کم آن نیاز به فشردهسازی تا ۲۰۰ برابر سطح فشار معمول خود دارد تا امکان سوخت رسانی به خودرو برای مسافتهای طولانیتر را داشته باشد. با وجود چنین فشار بالایی در سیستم سوخت رسانی CNG مخازن فلزی یا کامپوزیت که برای این فشار عملیاتی طراحی شدهاند الزامات ایمنی بالایی را ایجاب میکند. مخازن تولید شده با چنین امکانی در جهان اصولا به چهار دسته تقسیم میشوند:
- نوع اول تمام فلزی
- نوع دوم با آستر فلزی و ۴۵درصد کامپوزیت
- نوع سوم با آستر فلزی و 80درصد کامپوزیت
- نوع چهارم صد درصد کامپوزیت
انواع روشهای تولید مخزن
همان گونه که در زیر خواهد آمد تولید مخازن نوع اول به سه روش انجام می گیرد. شرکت آسیا ناما قادر به تولید مخازن به دوشیوه از سه شیوه ممکن است که به اختصار روش تولید هر کدام از شیوهها اشاره خواهد شد.
روش اول:
1- استفاده از شمش(billet)
در این روش تولید مخازن CNG، شمش فولادی از طریق فرایند اکستروژن به صورت کاپ در آمده و سپس سر این کاپها توسط فرایند فرم دهی گرم شکل دهی میگردد.
2- استفاده از لوله (pipe)
در این روش پس از بریدن لوله خام به اندازههای مورد نیاز، انتها و سر لوله توسط فرایند فرمدهی گرم شکلدهی میشود.
3- استفاده از ورق (plate)
در این روش تولید مخازن CNG ابتدا یک ورق گرد به اندازه مورد نیاز بریده شده و سپس توسط پرسهایی در چندین مرحله مورد کشش عمیق (کشش سرد) قرار میگیرد و کاپ تولید میگردد. سپس توسط فرایند فرمدهی گرم سر این کاپها بسته میشود.
مزیت تولید مخزن از ورق
استفاده از ورق برای تولید مخازن بدون درز CNG با روش فوق مزایایی را در بر دارد که در این قسمت به آنها اشاره میکنیم.
با توجه به روش تولید و مواد اولیه مورد نیاز، مزایای تولید مخازن با استفاده از ورق عبارتند از:
امکان استفاده از خط تولید با فناوری قابل دسترس جهت تولید بدنه استوانهای شکل:
خط تولید در این روش عموما از پرسهای هیدرولیک و قالبهای کشش تشکیل میشود و در حال حاضر صنایع مختلف فعال در کشور از این تجهیزات استفاده نموده و حتی قابلیت تولید آن را نیز دارند.
امکان تهیه مواد اولیه در داخل کشور: هم اکنون صنایع فولاد سازی انواع ورقهای مختلف را تولید میکنند و امکان تولید ورقهای مورد نیاز در کشور میسر است.
قابلیت انبارش بیشتر مواد اولیه: نظر به این که امکان قرار دادن ورقهای فولادی به صورت بستهای روی یکدیگر بیشتر از سایر مواد اولیه میباشد، در این روش به مساحت انبار کمتری نیاز میباشد.
امکان جابهجایی و حمل و نقل آسان تر مواد اولیه: با توجه به این که امکان جا به جایی و راندمان حمل و نقل ورقهای فولادی بالاتر از لولههای بدون درز میباشد هزینه حمل و نقل خارج از کارخانه کمتر بوده و جابهجایی آنها در داخل کارخانه نیز با سهولت بیشتری انجام خواهد شد.
ارزانتر بودن مواد اولیه: با توجه به این که تولید لولههای فولادی بدون درز مورد استفاده در ساخت مخازن در انحصار چند شرکت معدود خارجی میباشد، امکان تهیه ارزانتر ورقهای فولادی در داخل و یا حتی واردات آنها با بهای کمتر وجود دارد.
امکان دست یابی به دقتهای بالاتر در محصولات: نظر به این که خط تولید در این روش صرفا جهت تولید مخازن CNG طراحی میشود و در مقابل تولید کنندگان لولههای بدون درز محصولات خود را جهت استفادههای عام تولید میکنند، تلرانسهای مد نظر در استانداردهای تولید این مخازن در روش تولید با ورق کاملا قابل رعایت است.
امکان تولید کاپ به عنوان مواد اولیه کارخانجات کشور
با توجه به عدم نیاز به واردات لوله به عنوان مواد اولیه، خودکفایی در زمینه تولید این محصول فراهم میگردد.
سبکتر بودن مخازن تولید شده: در این روش امکان دسترسی به حداقل ضخامت استاندارد جداره مخازن به علت بستهتر بودن تلرانسهای اعمال شده بر پروفیل مخازن بیشتر است. لذا مخازن تولید شده دارای وزن کمتری نسبت به نوع مشابه تولید شده ازلوله میباشند. از آنجا که سبک تر بودن مخازن استفاده شده در خورو دارای مزایا فراوانی است تولید با این روش مناسبتر میباشد. از مزایای سبک تر بودن مخازن میتوان به موارد زیر اشاره نمود:
کاهش مصرف ترمز خودرو
کاهش مصرف سوخت
بهبود سیستم تعلیق خودرو
یکنواختی ضخامت به علت کشش عمیق در تولید مخازن از ورق (در ورق نوسان ضخامت ۰.۲ میلیمتر و در لوله ۰.۶ میلیمتر میباشد).
حداقل استحکام کششی قابل حصول در مخازن تولیدی از ورق: 1000 مگاپاسکال
حداقل استحکام کششی قابل حصول در مخازن تولیدی از لوله: ۹۵۵مگاپاسکال
عدم نشتی از انتهای مخزن را میتوان به عنوان یکی از مهمترین مزیتهای روش تولید از ورق در تولید این نوع مخازن نام برد. به همین خاطر در استاندارد ISO ۱۱۴۳۹ در روش تولیدی از لوله، به دلیل فرم دهی انتهای مخزن، سازنده را ملزم به تستهای غیر مخرب نموده است، ولی در روش تولیدی از ورق به دلیل بالا بودن اطمینان از عدم نشتی و بالا بودن ایمنی نیازی به این تست نمیباشد.استاندارد ISO ۱۱۴۳۹ یک تست پنوماتیکی را برای مخازن تولیدی از لوله به دلیل فرم دهی گرم انتهای مخزن در نظر گرفته است که طبق آن میبایست حد اقل ۲/ ۳ فشار کاری مخزن با هوا تست گردد در صورتی که برای مخازن تولیدی از ورق به این تست نیازی نمیباشد.
مقایسه کیفیت تولید مخازن تولیدی از روش لوله و ورق
اطمینان از ۱۰۰درصد عدم نشتی مخزن از انتها در روش تولید از ورق
انتهای مخازن تولیدی از ورق با کیفیت بالا و بدون نیاز به پروسههای اضافی جهت یکنواخت کردن انتهای مخزن
انتهای مخازن تولیدی از لوله نیاز به پروسههای اضافی جهت یکنواخت کردن انتهای مخزن و زائدههای آن ندارد.
ارسال نظر