یزد تایر، پیشگام در عرصه کیفیت و بهرهوری - ۶ خرداد ۹۲
بهره وری یکی از مهمترین مقولههای صنعت در جهت دستیبابی به حداکثر استفاده از توان و ظرفیت واحد تولیدی بوده و ماندگاری بنگاه اقتصادی ، تداوم تولید و مشتری مداری واحد در گروی بهره برداری بهینه از منابع بنگاه میباشد.
. در جهت بهبود و افزایش بهرهوری در مجتمع صنایع لاستیک یزد توجه به آموزش بعنوان یکی از ارکان اصلی ارتقاء بهرهوری در اولویت برنامههای شرکت قرار گرفته و با استفاده از خدمات آموزش درون و برون سازمانی در جهت افزایش مهارتهای فنی مرتبط با کار کارکنان مورد توجه خاص قرار گرفته است . همچنین اتوماسیون ماشین آلات و بهینه سازی خطوط تولید در جهت به حداقل رساندن خطای انسانی و افزایش کیفی محصولات درجهت جلب رضایت مشتری انجام پذیرفته و نیز توجه به تکنولوژی و بروز رسانی فن آوری تولید محصولات در این شرکت با استفاده از براند مشترک «وردشتاین» یزد تایردر جهت تولید تایرهای سیمی سری V که بعنوان اولین بار در کشور با هدف «صادرات محوری» انجام میپذیرد علاوه بر تامین نیاز داخل کشور بازارهای صادراتی ویژه ای را برای شرکت همراه خواهد داشت.
. در جهت بهبود و افزایش بهرهوری در مجتمع صنایع لاستیک یزد توجه به آموزش بعنوان یکی از ارکان اصلی ارتقاء بهرهوری در اولویت برنامههای شرکت قرار گرفته و با استفاده از خدمات آموزش درون و برون سازمانی در جهت افزایش مهارتهای فنی مرتبط با کار کارکنان مورد توجه خاص قرار گرفته است . همچنین اتوماسیون ماشین آلات و بهینه سازی خطوط تولید در جهت به حداقل رساندن خطای انسانی و افزایش کیفی محصولات درجهت جلب رضایت مشتری انجام پذیرفته و نیز توجه به تکنولوژی و بروز رسانی فن آوری تولید محصولات در این شرکت با استفاده از براند مشترک «وردشتاین» یزد تایردر جهت تولید تایرهای سیمی سری V که بعنوان اولین بار در کشور با هدف «صادرات محوری» انجام میپذیرد علاوه بر تامین نیاز داخل کشور بازارهای صادراتی ویژه ای را برای شرکت همراه خواهد داشت.
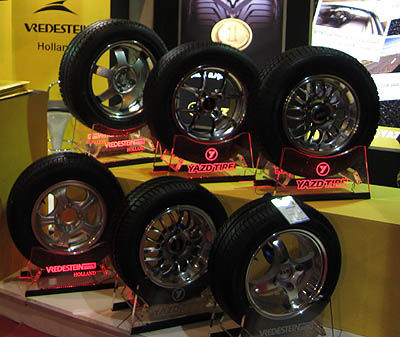
بهره وری یکی از مهمترین مقولههای صنعت در جهت دستیبابی به حداکثر استفاده از توان و ظرفیت واحد تولیدی بوده و ماندگاری بنگاه اقتصادی ، تداوم تولید و مشتری مداری واحد در گروی بهره برداری بهینه از منابع بنگاه میباشد.
. در جهت بهبود و افزایش بهرهوری در مجتمع صنایع لاستیک یزد توجه به آموزش بعنوان یکی از ارکان اصلی ارتقاء بهرهوری در اولویت برنامههای شرکت قرار گرفته و با استفاده از خدمات آموزش درون و برون سازمانی در جهت افزایش مهارتهای فنی مرتبط با کار کارکنان مورد توجه خاص قرار گرفته است . همچنین اتوماسیون ماشین آلات و بهینه سازی خطوط تولید در جهت به حداقل رساندن خطای انسانی و افزایش کیفی محصولات درجهت جلب رضایت مشتری انجام پذیرفته و نیز توجه به تکنولوژی و بروز رسانی فن آوری تولید محصولات در این شرکت با استفاده از براند مشترک «وردشتاین» یزد تایردر جهت تولید تایرهای سیمی سری V که بعنوان اولین بار در کشور با هدف «صادرات محوری» انجام میپذیرد علاوه بر تامین نیاز داخل کشور بازارهای صادراتی ویژه ای را برای شرکت همراه خواهد داشت.
پروژههای ارائه شده به جشنواره ملی بهرهوری نیز با هدف افزایش و بهبود بهرهوری با مدیریت همکاران ارجمند مجتمع صنایع لاستیک یزد آقایان:
مهندس محمد رضا شایق، معاون فنی
مهندس منوچهر بهشت آرا، مدیر تولید و پروژه رادیال
مهندس علی اصغر بابایی، مدیر تکنیکال
مهندس جلال مجری، مدیر تحقیق و توسعه
انجام پذیرفته که خلاصه ای ازپروژهها به شرح ذیل است:
موفقیت مجتمع صنایع لاستیک یزد ( یزد تایر ) نتیجه توجه به آموزش نیروی انسانی ، بهبود مستمر، تحقیق و توسعه، اتوماسیون ماشین آلات تولیدی و ارتقاء تکنولوژی در جهت افزایش بهرهوری تولید بوده است
پروژه شماره ۱
عنوان پروژه : ارتقاء تکنولوژی و کارایی پرسهای پخت تایر
مقدمه:
باتوجه به تغییر الگوی مصرف از تایرهای نخی به رادیال سیمی و به منظور جلوگیری از رکود و باقی ماندن در بازار رقابت و شرایط سخت خرید ماشین آلات از خارج در موقعیت تحریم، اصلاح و تبدیل پرسهای از رده خارج شده پخت تایر بایاس به پرسهای پخت تایر رادیال در الویت فعالیتهای سازمان قرار گرفت.
از آنجاییکه محدودیت زمان و منابع مالی و تحریمهای شرکتهای اروپایی وجود داشت در صورت عدم اقدام بموقع این شرکت، مانند برخی دیگر از کارخانههای تایرسازی دچار مشکلات تولیدی و مالی می گردید .
هدف:
۱- حفظ و بقای شرکت در بازار ایران و منطقه
2- افزایش سهم بیشتری از بازار تایر
۳- مطرح شدن برند یزد تایر بعنوان با کیفیت ترین تایر رادیال ایرانی
4- افزایش تخصص و کارایی پرسنل فنی کارخانه
۵- کاهش و حذف وابستگی به شرکتهای خارجی در تامین ماشین آلات و قطعات
6- جلوگیری از خروج ارز از کشور
اقدامات انجام شده:
با مطالعه همه جانبه و تغییر طراحی در پرسهای پخت تایرهای بایاس که به لحاظ از رده خارج شدن محصولات آن بلااستفاده مانده بود عمل تبدیل این پرسها به پرسهایی با قابلیت پخت تایرهای رادیال با موفقیت چشمگیر انجام گرفت.
دستاوردهای حاصله دراین زمینه شامل موارد زیر است:
1. جلوگیری از واردات سالانه حدود 7000 تن تایر به کشور و صرفه جویی حدود 30000000 دلار ارزبری.
۲. جلوگیری از خروج رقم قابل توجهی یورو ارز جهت خرید پرس پخت تایر.
3. بومی شدن صنعت ساخت پرس پخت تایر و قطع وابستگی در این زمینه و عدم نیاز به تامین قطعات.
۴.افزایش روحیه خودباوری و اعتماد به نفس و تحقق شعار ما میتوانیم.
پروژه شماره ۲
عنوان پروژه: تولید تایرهای رادیال سواری با سایزو طرح جدید
مقدمه:
با شروع فاز دوم پروژه رادیال با هدف افزایش توان تولید روزانه از ۲۴تن به ۵۲تن، همگام با خرید ماشین آلات و نصب و راهاندازی آنها با توجه به کمبود قالبهای پخت تایرهای رادیال سواری، لازم بود قسمتی از کسری قالبها با تکثیر قالبهای پرمصرف بازار و بخشی دیگر با طراحی و ساخت قالبهای تایر با سایزهای جدید و طرحهای نو تکمیل گردد.
هدف:
تولید طرح جدیدی از تایر رادیال که حاصل ارزیابی و بررسی بازار،نظرات نمایندگان محترم و خواستههای مشتریان گرامی بویژه خودروسازان داخلی باشد.
اقدام انجام شده:
به منظور رسیدن به هدف تعیین شده برای دو سایز تایر، مراحل طراحی، سفارش و ساخت قالب، تولید آزمایشی انجام و در خط تولید انبوه قرار گرفت. تایرهای انتخاب شده، درزمره تایرهای وارداتی بوده و در داخل کشور تولید نمی شد و مجتمع صنایع لاستیک یزد اولین تولیدکننده داخلی در کشور میباشد.
این تایرها عبارتند از:
1) 205/60R14 - 88H / Mercury
۲۰۵/۶۰R۱۵ - ۹۱H / Mercury (۲
دستاوردهای حاصله دراین زمینه شامل موارد زیر است:
1- جلب رضایت هرچه بیشتر مشتریان،حفظ و افزایش سهم بازار فروش.
۲- تداوم تولید تایرهای رادیال جدیددرشرکت.
3-اجرای این پروژه تنوع سایز در تایرهای رادیال شرکت را افزایش میداد،درنتیجه دامنه وگستره برنامه ریزی تولید را بازتر و مشتریان بیشتری را جذب محصولات شرکت میکرد.
۴- نشانده پویایی شرکت یزد تایر در زمینه توسعه وتحقیق بود.
5- بهترین انتخاب برای افزایش توان تولید تایرهای رادیال شرکت یزدتایربود.
۶- حمایت از تولیدات داخلی بویژه صنعت تایر ایران و کاهش واردات برخی از سایزهای تایر رادیال.
7- ایجاد فعالیت اقتصادی در واحدهای صنعتی بویژه قالب سازی.
۸- جذب نیروهای اپراتور ماهر در خط تولید.
9- تنوع در سبدهای فروش محصولات وامکان انتخاب بیشتر برای مشتریان تایرهای رادیال.
۱۰- درخواست وتقاضای بیشتر برای این سایزها وتولید مستمرآنهاوپوشش فرصتهاوظرفیت خالی ماشین آلات.
پروژه شماره۳
عنوان پروژه: افزایش بهرهوری تیوب از طریق بازنگری در طراحی آمیزه
مقدمه:
کاهش وابستکی مواد اولیه تولید تیوب به خارج و همچنین بهبود خواص فیزیکی و مکانیکی تیوب با استفاده از کائوچوی EPDM علاوه بر اینکه باعث کاهش قیمت و کاهش وابستگی به مواد اولیه خارجی میگردد باعث افزایش خواص فیزیکی تیوب از جمله مقاومت در برابر حمله ازون، بهبود مقاومت حرارتی، بهبود استحکام خام تیوب، کاهش تورم قالبی، افزایش چسبندگی محل اسپلایس میگردد.
هدف:
با توجه به مشکل Ozone Crack تیوب در محل تاخوردگی و در نتیجه تخریب تیوب استفاده از EPDM برای حل این مشکل ضروری میباشد همچنین بهبود مقاومت حرارتی در سرویس نیز مزیت دیگر این جایگزینی میباشد.
انجام کار تحقیقاتی به منظور بهبود پارامترهایی که در عملکرد تیوب موثر بوده و عبارتند از :
الف- استحکام کششی
ب- ازدیاد طول در نقطه پارگی
ج- استحکام کششی در 300 درصد افزایش طول
د- سختی آمیزه تیوب در واحد Shore A
ه -مقاومت خواص فیزیکی تیوب در برابر حرارت
اقدام انجام شده و دستاوردهای حاصله دراین زمینه شامل موارد زیر است:
استفاده از ریکلیم بیوتیلی و EPDM به ازاء هر کیلوگرم ۳/۰ دلار صرفه جویی ارزی و در نتیجه موجب ۷۴۵۳ ریال کاهش قیمت بدنبال خواهد داشت . با توجه به ظرفیت تولید روزانه حدود ۱۰ تن تیوب، صرفه جویی ارزی ناشی از این تغییر، سالانه حدود ۱.۰۵۰.۰۰۰ دلار خواهد بود.
همچنین بکارگیری ریکلیم و EPDM در آمیزه تیوب موارد ذیل را بهبود بخشید:
-کاهش تورم قالبی و در نتیجه افزایش یکنواختی تیوب
-جلوگیری از نازک شدن گوشههای تیوب
- افزایش چسبندگی تیوب خام
- افزایش استحکام محل اسپلایس تیوب
علاوه بر موارد فوق به کارگیری EPDM مشکل ترکهای ازونی در تیوب، بهبود قابل ملاحظهای یافت و با عملی شدن توجیه اقتصادی آن باعث اشتغال زایی حدود 100 نفر و جلوگیری از ورود تیوب خارجی به داخل و خروج ارز که در این سالها برای کشور یک مسئله حیاتی است، عملاً سیاست اقتصاد مقاومتی در دستور کار قرار گرفت.
پروژه شماره ۴
عنوان پروژه: کاهش قیمت تمام شده و بهبود کیفیت تایرهای رادیال از طریق بازنگری در طراحی
مقدمه :
مشکلات اقتصادی ناشی از تحریمهای جهانی و افزایش نرخ ارز و بالا رفتن هزینه خرید مواد اولیه خارجی (بخصوص کائوچوی طبیعی) و سایر هزینهها ، موجب تغییر قیمت تمام شده محصولات تایر رادیال شده است، لذا حاشیه سود مطلوب و در نتیجه میزان بهرهوری کاهش یافته است.
تکنولوژی اولیه تولید تایرهای رادیال یزد از شرکت فردشتاین هلند اخذ شده اما اکنون پس از گذشت چند سال از زمان ورود تایرها به بازار، دادههای بدست آمده از ارزیابی فرایند و بازار، حاکی از آن است که یک سری بهبودهای کیفیتی جهت انطباق بیشتر ساختار و عملکرد تایر با شرایط خاص آب و هوایی ایران مورد نیاز میباشد. این بهبودها باید از طریق بازنگری جزئی در طراحی تایرها صورت پذیرند.
هدف: طرح این مسئله در سازمان و تعریف و اجرای پروژه مربوط به آن، دستآوردهای زیررا برای سازمان به همراه خواهد داشت:
1- افزایش بهرهوری از طریق کاهش هزینههای تولید
۲- افزایش بهرهوری از طریق افزایش سهم بازار فروش
3- کاهش وابستگی به خارج
۴- برداشتن گامی موثر در راستای اقتصاد مقاومتی
اقدام انجام شده:
۱- با طراحی مجدد و ساخت قالب ، مشکل ترک خوردگی در تایرهای ۲۰۵/۶۰ R۱۴ و ۲۰۵/۶۰ R۱۵ مرتقع گردید. پروفایل جدید دارای ضخامت و پهنای اپتیمم، وزن مناسب و کاملا متناسب با نیازهای کاربردی تایر بود. در پروفایل جدید مشکل ترک خوردگی کاملاً برطرف شد.
2- برای رفع مشکل غرکردگی موضعی در تایرهای 165/80 R13 و 175/70 R13 با انجام یکسری محاسبات مهندسی محصول، از یک نمونه نخ جدید در ساختار لایه داخلی تایر استفاده شد که تعداد آن در هر ده سانتیمتر 28 عدد بیشتر و ضخامت 0.1 mm کمتر که در مجموع استحکام اولیه و مورد نیاز تایر را فراهم میکرد. استفاده از این نخ مشکل غرکردگی موضعی را برطرف ساخت.
دستاوردهای حاصله دراین زمینه شامل موارد زیر است:
1-مشکلات کیفی موجود در چند سایز از محصولات برطرف گردیدند.
۲- با انجام اصلاحات کیفیتی وزن محصولات به صورت قابل ملاحظه ای کاهش یافته است.
3- این اصلاحات صرفه جویی سالیانه 1868 تن کائوچوی طبیعی و 6114534048 ریال را برای شرکت موجب شده و از سطح وابستگی به این ماده خارجی و مشکلات مربوط به تامین آن کاسته شده است.
4- موارد فوق در مجموع میزان بهرهوری را در شرکت افزایش داده است.
. در جهت بهبود و افزایش بهرهوری در مجتمع صنایع لاستیک یزد توجه به آموزش بعنوان یکی از ارکان اصلی ارتقاء بهرهوری در اولویت برنامههای شرکت قرار گرفته و با استفاده از خدمات آموزش درون و برون سازمانی در جهت افزایش مهارتهای فنی مرتبط با کار کارکنان مورد توجه خاص قرار گرفته است . همچنین اتوماسیون ماشین آلات و بهینه سازی خطوط تولید در جهت به حداقل رساندن خطای انسانی و افزایش کیفی محصولات درجهت جلب رضایت مشتری انجام پذیرفته و نیز توجه به تکنولوژی و بروز رسانی فن آوری تولید محصولات در این شرکت با استفاده از براند مشترک «وردشتاین» یزد تایردر جهت تولید تایرهای سیمی سری V که بعنوان اولین بار در کشور با هدف «صادرات محوری» انجام میپذیرد علاوه بر تامین نیاز داخل کشور بازارهای صادراتی ویژه ای را برای شرکت همراه خواهد داشت.
پروژههای ارائه شده به جشنواره ملی بهرهوری نیز با هدف افزایش و بهبود بهرهوری با مدیریت همکاران ارجمند مجتمع صنایع لاستیک یزد آقایان:
مهندس محمد رضا شایق، معاون فنی
مهندس منوچهر بهشت آرا، مدیر تولید و پروژه رادیال
مهندس علی اصغر بابایی، مدیر تکنیکال
مهندس جلال مجری، مدیر تحقیق و توسعه
انجام پذیرفته که خلاصه ای ازپروژهها به شرح ذیل است:
موفقیت مجتمع صنایع لاستیک یزد ( یزد تایر ) نتیجه توجه به آموزش نیروی انسانی ، بهبود مستمر، تحقیق و توسعه، اتوماسیون ماشین آلات تولیدی و ارتقاء تکنولوژی در جهت افزایش بهرهوری تولید بوده است
پروژه شماره ۱
عنوان پروژه : ارتقاء تکنولوژی و کارایی پرسهای پخت تایر
مقدمه:
باتوجه به تغییر الگوی مصرف از تایرهای نخی به رادیال سیمی و به منظور جلوگیری از رکود و باقی ماندن در بازار رقابت و شرایط سخت خرید ماشین آلات از خارج در موقعیت تحریم، اصلاح و تبدیل پرسهای از رده خارج شده پخت تایر بایاس به پرسهای پخت تایر رادیال در الویت فعالیتهای سازمان قرار گرفت.
از آنجاییکه محدودیت زمان و منابع مالی و تحریمهای شرکتهای اروپایی وجود داشت در صورت عدم اقدام بموقع این شرکت، مانند برخی دیگر از کارخانههای تایرسازی دچار مشکلات تولیدی و مالی می گردید .
هدف:
۱- حفظ و بقای شرکت در بازار ایران و منطقه
2- افزایش سهم بیشتری از بازار تایر
۳- مطرح شدن برند یزد تایر بعنوان با کیفیت ترین تایر رادیال ایرانی
4- افزایش تخصص و کارایی پرسنل فنی کارخانه
۵- کاهش و حذف وابستگی به شرکتهای خارجی در تامین ماشین آلات و قطعات
6- جلوگیری از خروج ارز از کشور
اقدامات انجام شده:
با مطالعه همه جانبه و تغییر طراحی در پرسهای پخت تایرهای بایاس که به لحاظ از رده خارج شدن محصولات آن بلااستفاده مانده بود عمل تبدیل این پرسها به پرسهایی با قابلیت پخت تایرهای رادیال با موفقیت چشمگیر انجام گرفت.
دستاوردهای حاصله دراین زمینه شامل موارد زیر است:
1. جلوگیری از واردات سالانه حدود 7000 تن تایر به کشور و صرفه جویی حدود 30000000 دلار ارزبری.
۲. جلوگیری از خروج رقم قابل توجهی یورو ارز جهت خرید پرس پخت تایر.
3. بومی شدن صنعت ساخت پرس پخت تایر و قطع وابستگی در این زمینه و عدم نیاز به تامین قطعات.
۴.افزایش روحیه خودباوری و اعتماد به نفس و تحقق شعار ما میتوانیم.
پروژه شماره ۲
عنوان پروژه: تولید تایرهای رادیال سواری با سایزو طرح جدید
مقدمه:
با شروع فاز دوم پروژه رادیال با هدف افزایش توان تولید روزانه از ۲۴تن به ۵۲تن، همگام با خرید ماشین آلات و نصب و راهاندازی آنها با توجه به کمبود قالبهای پخت تایرهای رادیال سواری، لازم بود قسمتی از کسری قالبها با تکثیر قالبهای پرمصرف بازار و بخشی دیگر با طراحی و ساخت قالبهای تایر با سایزهای جدید و طرحهای نو تکمیل گردد.
هدف:
تولید طرح جدیدی از تایر رادیال که حاصل ارزیابی و بررسی بازار،نظرات نمایندگان محترم و خواستههای مشتریان گرامی بویژه خودروسازان داخلی باشد.
اقدام انجام شده:
به منظور رسیدن به هدف تعیین شده برای دو سایز تایر، مراحل طراحی، سفارش و ساخت قالب، تولید آزمایشی انجام و در خط تولید انبوه قرار گرفت. تایرهای انتخاب شده، درزمره تایرهای وارداتی بوده و در داخل کشور تولید نمی شد و مجتمع صنایع لاستیک یزد اولین تولیدکننده داخلی در کشور میباشد.
این تایرها عبارتند از:
1) 205/60R14 - 88H / Mercury
۲۰۵/۶۰R۱۵ - ۹۱H / Mercury (۲
دستاوردهای حاصله دراین زمینه شامل موارد زیر است:
1- جلب رضایت هرچه بیشتر مشتریان،حفظ و افزایش سهم بازار فروش.
۲- تداوم تولید تایرهای رادیال جدیددرشرکت.
3-اجرای این پروژه تنوع سایز در تایرهای رادیال شرکت را افزایش میداد،درنتیجه دامنه وگستره برنامه ریزی تولید را بازتر و مشتریان بیشتری را جذب محصولات شرکت میکرد.
۴- نشانده پویایی شرکت یزد تایر در زمینه توسعه وتحقیق بود.
5- بهترین انتخاب برای افزایش توان تولید تایرهای رادیال شرکت یزدتایربود.
۶- حمایت از تولیدات داخلی بویژه صنعت تایر ایران و کاهش واردات برخی از سایزهای تایر رادیال.
7- ایجاد فعالیت اقتصادی در واحدهای صنعتی بویژه قالب سازی.
۸- جذب نیروهای اپراتور ماهر در خط تولید.
9- تنوع در سبدهای فروش محصولات وامکان انتخاب بیشتر برای مشتریان تایرهای رادیال.
۱۰- درخواست وتقاضای بیشتر برای این سایزها وتولید مستمرآنهاوپوشش فرصتهاوظرفیت خالی ماشین آلات.
پروژه شماره۳
عنوان پروژه: افزایش بهرهوری تیوب از طریق بازنگری در طراحی آمیزه
مقدمه:
کاهش وابستکی مواد اولیه تولید تیوب به خارج و همچنین بهبود خواص فیزیکی و مکانیکی تیوب با استفاده از کائوچوی EPDM علاوه بر اینکه باعث کاهش قیمت و کاهش وابستگی به مواد اولیه خارجی میگردد باعث افزایش خواص فیزیکی تیوب از جمله مقاومت در برابر حمله ازون، بهبود مقاومت حرارتی، بهبود استحکام خام تیوب، کاهش تورم قالبی، افزایش چسبندگی محل اسپلایس میگردد.
هدف:
با توجه به مشکل Ozone Crack تیوب در محل تاخوردگی و در نتیجه تخریب تیوب استفاده از EPDM برای حل این مشکل ضروری میباشد همچنین بهبود مقاومت حرارتی در سرویس نیز مزیت دیگر این جایگزینی میباشد.
انجام کار تحقیقاتی به منظور بهبود پارامترهایی که در عملکرد تیوب موثر بوده و عبارتند از :
الف- استحکام کششی
ب- ازدیاد طول در نقطه پارگی
ج- استحکام کششی در 300 درصد افزایش طول
د- سختی آمیزه تیوب در واحد Shore A
ه -مقاومت خواص فیزیکی تیوب در برابر حرارت
اقدام انجام شده و دستاوردهای حاصله دراین زمینه شامل موارد زیر است:
استفاده از ریکلیم بیوتیلی و EPDM به ازاء هر کیلوگرم ۳/۰ دلار صرفه جویی ارزی و در نتیجه موجب ۷۴۵۳ ریال کاهش قیمت بدنبال خواهد داشت . با توجه به ظرفیت تولید روزانه حدود ۱۰ تن تیوب، صرفه جویی ارزی ناشی از این تغییر، سالانه حدود ۱.۰۵۰.۰۰۰ دلار خواهد بود.
همچنین بکارگیری ریکلیم و EPDM در آمیزه تیوب موارد ذیل را بهبود بخشید:
-کاهش تورم قالبی و در نتیجه افزایش یکنواختی تیوب
-جلوگیری از نازک شدن گوشههای تیوب
- افزایش چسبندگی تیوب خام
- افزایش استحکام محل اسپلایس تیوب
علاوه بر موارد فوق به کارگیری EPDM مشکل ترکهای ازونی در تیوب، بهبود قابل ملاحظهای یافت و با عملی شدن توجیه اقتصادی آن باعث اشتغال زایی حدود 100 نفر و جلوگیری از ورود تیوب خارجی به داخل و خروج ارز که در این سالها برای کشور یک مسئله حیاتی است، عملاً سیاست اقتصاد مقاومتی در دستور کار قرار گرفت.
پروژه شماره ۴
عنوان پروژه: کاهش قیمت تمام شده و بهبود کیفیت تایرهای رادیال از طریق بازنگری در طراحی
مقدمه :
مشکلات اقتصادی ناشی از تحریمهای جهانی و افزایش نرخ ارز و بالا رفتن هزینه خرید مواد اولیه خارجی (بخصوص کائوچوی طبیعی) و سایر هزینهها ، موجب تغییر قیمت تمام شده محصولات تایر رادیال شده است، لذا حاشیه سود مطلوب و در نتیجه میزان بهرهوری کاهش یافته است.
تکنولوژی اولیه تولید تایرهای رادیال یزد از شرکت فردشتاین هلند اخذ شده اما اکنون پس از گذشت چند سال از زمان ورود تایرها به بازار، دادههای بدست آمده از ارزیابی فرایند و بازار، حاکی از آن است که یک سری بهبودهای کیفیتی جهت انطباق بیشتر ساختار و عملکرد تایر با شرایط خاص آب و هوایی ایران مورد نیاز میباشد. این بهبودها باید از طریق بازنگری جزئی در طراحی تایرها صورت پذیرند.
هدف: طرح این مسئله در سازمان و تعریف و اجرای پروژه مربوط به آن، دستآوردهای زیررا برای سازمان به همراه خواهد داشت:
1- افزایش بهرهوری از طریق کاهش هزینههای تولید
۲- افزایش بهرهوری از طریق افزایش سهم بازار فروش
3- کاهش وابستگی به خارج
۴- برداشتن گامی موثر در راستای اقتصاد مقاومتی
اقدام انجام شده:
۱- با طراحی مجدد و ساخت قالب ، مشکل ترک خوردگی در تایرهای ۲۰۵/۶۰ R۱۴ و ۲۰۵/۶۰ R۱۵ مرتقع گردید. پروفایل جدید دارای ضخامت و پهنای اپتیمم، وزن مناسب و کاملا متناسب با نیازهای کاربردی تایر بود. در پروفایل جدید مشکل ترک خوردگی کاملاً برطرف شد.
2- برای رفع مشکل غرکردگی موضعی در تایرهای 165/80 R13 و 175/70 R13 با انجام یکسری محاسبات مهندسی محصول، از یک نمونه نخ جدید در ساختار لایه داخلی تایر استفاده شد که تعداد آن در هر ده سانتیمتر 28 عدد بیشتر و ضخامت 0.1 mm کمتر که در مجموع استحکام اولیه و مورد نیاز تایر را فراهم میکرد. استفاده از این نخ مشکل غرکردگی موضعی را برطرف ساخت.
دستاوردهای حاصله دراین زمینه شامل موارد زیر است:
1-مشکلات کیفی موجود در چند سایز از محصولات برطرف گردیدند.
۲- با انجام اصلاحات کیفیتی وزن محصولات به صورت قابل ملاحظه ای کاهش یافته است.
3- این اصلاحات صرفه جویی سالیانه 1868 تن کائوچوی طبیعی و 6114534048 ریال را برای شرکت موجب شده و از سطح وابستگی به این ماده خارجی و مشکلات مربوط به تامین آن کاسته شده است.
4- موارد فوق در مجموع میزان بهرهوری را در شرکت افزایش داده است.
ارسال نظر