مدیر عامل یک شرکت دانشبنیان عنوان کرد
تضمین حاشیه سود شرکتها با بومیسازی
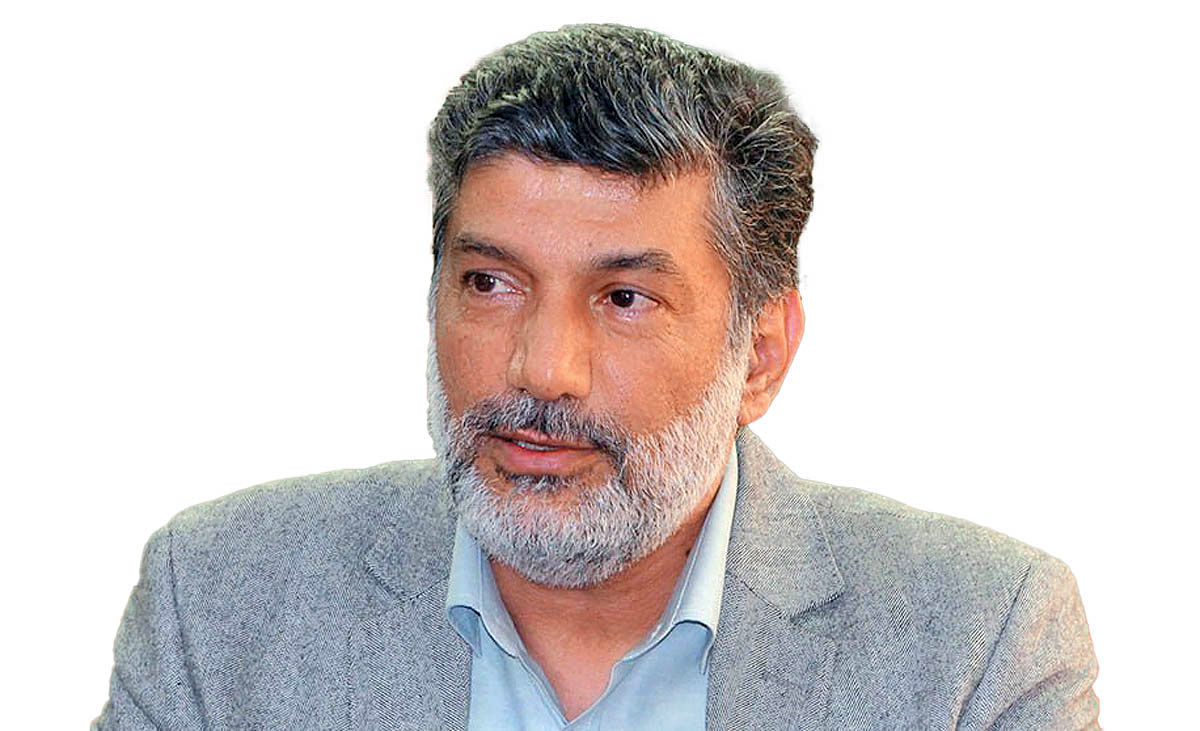
در این میان بومیسازی به مثابه ساخت داخل، تعریف ساده و سطحی بومیسازی است. تعریف کارشناسان صنعت از بومیسازی در واقع تحقق پتانسیل رشد صنعتی نهفته در داخل کشور و یافتن جایگاه شایسته در سلسله مراتب مزیت نسبی در دنیا است؛ ما و هیچ کشوری در دنیا با قطع ارتباطات بینالمللی منفعتی کسب نخواهیم کرد، اما این به معنای آن نیست که دانش، توان و منابعی را که در داخل کشور وجود دارد نیز از خارج وارد کنیم؛ واردات بیرویه دقیقا مانند این است که دانش، توان و منابعی را که خودمان در اختیار داریم از دیگران اخذ کنیم. بومیسازی در معنای کلی یک استراتژی و در معنای جزئی یک ابزار برای توسعه صنعتی محسوب میشود و محدود به شرایط تحریم نیست. یکی از شرکتهایی که طی سالهای اخیر به خوبی توانسته مفهوم دانشبنیانی و بومیسازی را عملیاتی کند شرکت دوده صنعتی پارس است که به تازگی در زمره شرکتهای دانشبنیان قرار گرفته است. برای پی بردن به روند حرکت این شرکت به سمت بومیسازی و دانشبنیانی علی کدخداشهریاری، مدیر عامل شرکت پاسخگوی سوالات ما بوده است .
به جز تامین نقدینگی،چالشهای اصلی روند پروژه چه بود و چگونه بر آنها فائق آمدید؟
طراحی پایه و تفصیلی مهندسان و متخصصان ایرانی در پروژه جایگزینی رآکتورهای هارد کارخانه دوده صنعتی پارس (فاز ۳ توسعه) سال گذشته پس از عبور از مسیر ناهموار تامین نقدینگی، تامین تجهیزات، ساخت، نصب، قوانین، دستورالعملها، تحریم، جنگ روسیه با اوکراین و ... در نهایت با راهاندازی جهادی توسط گروهی دیگر از متخصصان ایرانی در صنعت دوده، به بار نشست.
در این مسیر علاوه بر عزیزانی که بهصورت مستقیم در خط مقدم و پشتیبانی درگیر حل مسائل مختلف بودند، حمایت و همدلی مدیرعامل و اعضای هیات مدیره شرکتهای شستا، تاپیکو، سرمایهگذاری صنایع پتروشیمی(PIIC) و دوده صنعتی پارس در نتایج حاصله شایان توجه است و از همه عزیزان صمیمانه سپاسگزارم.
چه چیزی باعث این میزان از اهمیت برای این خط جدید و جایگزینی رآکتور جدید با رآکتورهای قدیمی است؟
راهاندازی فاز ۳ موجب بهبود کیفیت و افزایش تنوع و مقدار محصول در خط تولید دوده هارد شده است. با توجه به فرسودگی خطوط تولید در کارخانه تنها راه ادامه حیات شرکت و حفظ سهم بازار دوده صنعتی و همچنین حفظ و ارتقای کارکنان شریف آن، به ثمر نشستن این پروژه و راهاندازی آن بود. با توجه به شرایط سایر بخشها و خطوط تولید کارخانه، ادامه روند توسعه کارخانه برای حفظ شرایط پایدار تولید، ضروری است.
حرکت در عرصه تولید و رونق اقتصادی و اوج گرفتن ثروت ملی و رفاه عمومی در کشور، مثل همه عرصههای دیگر به پیشروانی، فرماندهی، صفوف مقدمی که این پیشروان و فرماندهان آن، تولیدکنندگان هستند احتیاج دارد. بر این اساس همه کارکنان شرکت دوده صنعتی پارس از اینکه در حیطه تولید فعالیت میکنند، به خود میبالند.
زمان انجام این پروژه مصادف با یکی از سختترین شرایط تحریمی کشور بود، چالشهای شما برای عبور از این شرایط چه بود؟
در تامین بخشی از تجهیزات این فاز با مسائل ناشی از تحریم دست به گریبان بودیم. قطعا کسی از وجود تحریمها لذت نمیبرد، ولی این تحریمها بخشی از جنگ اقتصادی ماست. کار اساسی مصونسازی اقتصاد کشور از آسیب دیدن از تحریم است؛ عبور از تحریم یک تاکتیک است، که استفاده میکنیم. ایجاد تنوع تولیدات، انتقال و توسعه دانش فنی محصولات نوین از راهکارهای موثر و کارآمد عرصه تولید در خنثیسازی تحریم هاست.
یکی از سختترین قسمتهای هر پروژه در ساختارهای دولتی و نیمه دولتی عبور از سد مجوزها و تاییدیههاست. آیا وجود این سد مانعی برای شما ایجاد نکرد؟
یکی از مسائل مهم در فاز ۳ تصمیمگیریهای متعدد در روند کار در شرایط موجود بود. خوشبختانه رویه مدیران و تصمیمگیران سابق و فعلی در هلدینگ سرمایهگذاری صنایع پتروشیمی، شرکت تاپیکو و مجموعه شستا بر ایجاد توسعه و افزایش بهرهوری و سودآوری جهت مالکان اصلی شرکت یعنی بازنشستگان و بیمهشدگان تامین اجتماعی است و نهایت همکاری و همدلی را در این زمینه فراهم آوردند. قطعا با تسهیل برخی قوانین میتوان به سرعتبخشی به جریان پروژههای مشابه کمک شایانی کرد.
تعدادی از مدیران در مجموعههای مشابه شما تمایلی به انجام پروژه توسعهای ندارند. چطور در حالی که بدون هیچ چالش عمدهای برای خود میتوانستید به فعالیت تولید ادامه دهید، به فکر ایجاد توسعه در شرکت افتادید؟
از نظر برخی «بیخطرترین کار، تصمیم نگرفتن است»، یکی از خطرناکترین فکرها همین فکر است که آدم بگوید: من اگر تصمیم بگیرم فلان دستگاه نظارتی این جوری میگوید، فلان مانعتراش این جوری میگوید، پس راحتتر این است که تصمیم نگیرم؛ باید تصمیم گرفت و اقدام کرد، باقیمانده موانع را باید برطرف کرد. چه بسیار مجموعههایی در کشور که با وجود زیانده بودن همچنان برای فرار از گرفتن تصمیمات سخت با وجود پتانسیلهای بالقوه فراوان، اقدام موثری برای برونرفت از شرایط نمیکنند.
استفاده از ظرفیتهای داخلی چه جایگاهی در این پروژه داشت؟
در فاز ۳ از ظرفیتهای متعدد داخلی حداکثر استفاده شد. چه در خدمات مهندسی چه در تامین مواد و ساخت تجهیزات در داخل، ظرفیتها خیلی بالا است، از تولید علم، فناوری، طراحی و مهندسی تا ساخت تجهیزات و... مهمترین قسمت کار که هسته مهندسی پروژه بود با استفاده از توان متخصصان علمی و فنی موجود در ایران انجام شد. مهندسی پایه و تفصیلی خط تولید دوده صنعتی برای اولین بار توسط متخصصان داخلی و قطعا با برداشت از دانش روز دنیا انجام شد. علاوه بر مهندسی، برخی از تجهیزات برای اولین بار در کشور ساخته شد. هر چند تا ساخت تمامی تجهیزات این صنعت در کشور فاصله داریم ولی نخبگان میتوانند روی اینها کار کنند و آنها را حل کنند. دوده صنعتی پارس از فعالیتهای علمی و عملی که در راستای کسب و کار دوده باشد، استقبال و در حد توان خود حمایت میکند.
مهمترین دستاورد شرکت شما در فاز جدید چه بود؟
فاز ۳ با دانش فنی متخصصان ایرانی و تجارب موجود، ایجاد شد و بر این اساس شرکت دوده صنعتی پارس برای ورود به جمع شرکتهای دانشبنیان اقدام کرد.
تجربه نشان داده که شرکتهای مطرح و صاحبنام خارجی به راحتی و به طور مستقیم حاضر به انتقال فناوریهای پایه و اساسی به کشور نیستند، بهخصوص در زمینههای اساسی نفت، خودرو، پتروشیمی. در این مسائل، دستگاههای داخلی باید به جد کشور و دستگاههای اجرایی را بینیاز کنند.
توجه کنیم که استفاده از دانش فنی شرکتهای خارجی و انتقال دانش فنی، منافعی را برای کشور در بر دارد و باید از آن بهره برد اما باید انتقال آن دانش به گونهای انجام شود که امکان جذب آن را داشته باشیم و برای حفظ و ارتقای دانش فنی زحمت بکشیم. اگر ما بایستیم بیتردید دانش خریداریشده قدیمی میشود، لذا نیاز به مدیریت و برنامهریزی اهل فن و هزینه کردن برای حفظ و ارتقای دانش فنی واقعی، اجرایی و ملموس داریم. نه اینکه توسعه دانش فقط محلی برای خرج کردن بودجه اختصاص داده شده باشد.
در مواردی هم که امکان خرید دانش فنی نیست، باید برای ایجاد آن برنامهریزی کنیم، بدیهی است که زمان و انرژی نیاز دارد، باید بلوغ این کار را پیدا کنیم. ما در شرکت دوده صنعتی پارس، قدم کوچکی برداشته تا در این راه حرکت کرده باشیم و راه بسیار طولانی را در پیش خواهیم داشت.
یادآور میشود شرکت دوده صنعتی پارس در سال ۱۳۶۳ ثبت شد و تولید دوده را از سال ۱۳۷۳ در ساوه، شهر صنعتی کاوه با ظرفیت ۱۵ هزار تن در سال آغاز کرده است. با بهرهبرداری از فاز دوم کارخانه در سال ۱۳۸۵، ظرفیت اسمی به ۳۰ هزار تن در سال رسید. در سال ۱۳۹۹، فاز سوم توسعه، با دانش فنی ایرانی جهت جایگزینی رآکتورهای تولید دوده هارد آغاز و در دیماه ۱۴۰۱ به بهرهبرداری رسید. اکنون با ۱۹۰ نفر پرسنل در کارخانه و دفتر مرکزی، انواع دودههای صنعتی N-۲۲۰, N-۲۳۴, N-۵۵۰, N-۶۶۰,N-۳۴۷, N-۳۳۰, N-۳۲۶, N-۳۳۹, N-۳۷۵ با استانداردهای بینالمللی در کارخانه دوده صنعتی پارس تولید میشود.